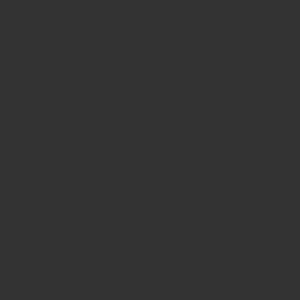
サイクルアップを目指し、成形条件の設定を変える際、どの設定を変更するでしょうか。ただ単に、冷却時間を短くするだけでは、冷却不足となり、取出しにより変形してしまいます。基本的には、樹脂を早く固めたいので、金型温度を下げたり、樹脂温度を下げるといった手段を取ると思います。
今回は、実際に失敗したことですが、金型温度を下げ、樹脂温度を下げた結果、期待したほどのサイクルアップが出来なかった点を、流動解析の分析内容をもとに、説明したいと思います。
モデルイメージ
モデルは、4個取りのピンゲートを採用しています(イメージ図)。
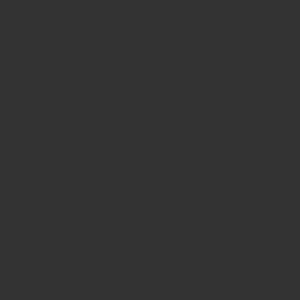
実成形の結果
普段の射出圧力は、圧力リミット70%でも余裕でしたが、サイクルテストでは圧力が70%付近まであがり、いつも以上の射出圧力がかかっていました。この時は、樹脂温度下げた分、少し流動しにくくなったのだろう、という程度の認識でリミット圧80%に上げテストを進めました。その後、サイクルもあまり縮まらず数秒の短縮で終わってしまい、目標値からほど遠い結果となってしまいました。
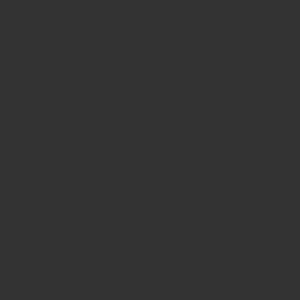
流動解析の確認
では、なぜ数秒しか短縮できなかったのか、流動解析から見てみます。流動解析でも、サイクルテストの条件では、射出圧力の上昇が示されていました。少し上がった程度なら特に気にしないのですが、この射出圧力が上がった結果、大きな弊害が発生していました。使用していた樹脂が、粘度の高いものであったこともありますが、サイクルテストでは、最高温度とせん断速度・最大が異常なまでの高さとなり、せん断に至っては、通常の100倍の値を示していました。
- 通常設定・・・普段の成形条件
- サイクルテスト設定・・・樹脂温度、型温を下げた成形条件(その他は、通常設定と同じ)
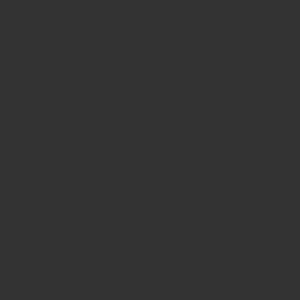
結局、このせん断発熱により樹脂温度が上昇したことで、サイクル短縮の効果が薄れてしまっています。
製品の同じ地点での固化率を、通常とサイクルテストで比較すると、サイクルテストでは数秒しか短くなっておらず、解析結果は、実際に行ったテストの結果と一致しています。それでも、数秒短縮できたのは、金型温度を下げたおかげだと考えます。
まとめ
いかがたっだでしょうか。金型温度を下げた効果はサイクル短縮に効果がありましたが、樹脂温度を下げた効果は逆にサイクルを伸ばす方向となってしまいました。温度によって、粘度変化の大きい樹脂では、樹脂温度を変化させる際、慎重に行わなければなりません。この失敗から、成形機から得られる圧力と速度のグラフは、改めて大事だと気づかされました。