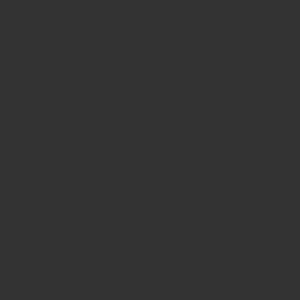
トンネルゲートは、型開きと同時に自動でゲートカットされるため、ゲートカット作業の手間が省けます。この点では、サイドゲートより便利な点ですが、欠点も存在します。サイドゲートよりも成形条件幅が狭くなりやすいです。また、製品内圧が足りないことで、製品表面の転写不足などが起き、条件の変更のみでは対応できない場合があります。
そこで、トンネルゲートの欠点に関して、流動解析の観点からご紹介します。
トンネルゲートの基本
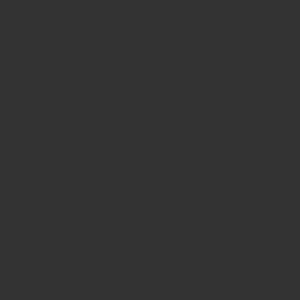
サブマリンゲートとも呼びます。2プレートタイプの金型で利用され、製品離型時に自動で、製品とランナーが分離されます。ゲートカットの不要な便利なゲートモデルですが、ランナーをしならせて無理抜きするため、ゲートカスが問題となることもあります。
トンネルゲートの欠点
1)せん断発熱
せん断発熱は、摩擦熱によって発生する熱であり、無理に射出速度を上げると、金型と樹脂との間で摩擦が大きくなり、発熱量が増えます。また、射出速度を抑えたとしても、樹脂が流路の狭い箇所を流れると、同様に摩擦が大きくなり、発熱が増えます。
製品やランナーを設計する上で、一般的にゲートが一番細くなります。せん断発熱が大きくなりすぎると、樹脂温度の上昇により、樹脂が劣化する可能性があります。そのため、各樹脂毎にせん断速度の上限があります。この上限を超えない範囲で、成形条件を決める必要があります。樹脂の劣化としては、目に見えるものとして、焼けがあります。焼けが発生すれば、外観上に問題が出ているため、成形オペレーターも気づき、射出速度を下げるでしょう。しかし、外観上見えない劣化の場合、製品の機能検査で発覚することになります。物性要求の厳しい製品では、注意が必要です。設計段階での試作で決定した成形条件を変更する場合は、しっかり機能テストまで行うほうが賢明だと思います。
また、せん断発熱が大きくなり、樹脂温度の上昇が大きくなると、樹脂の流動性が高くなるため(シャバシャバな樹脂)、金型の隙間に樹脂が入りやすくなり、バリが発生しやすくなります。
2)製品内圧の不足
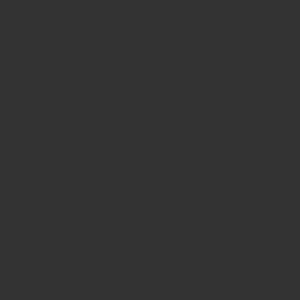
トンネルゲートのように、ゲート径が小さいと、思った以上に製品内圧が低くなります。保圧の圧力が大きく損失し、製品内部に届きます。必ずしも圧力の損失が大きくなるというわけではありませんが、多数個取り、ランナー流路が長い、ゲートが小さいという条件がそろうと、圧力損失が大きくなります。また、低い保圧であるほど、圧力損失は増大します。
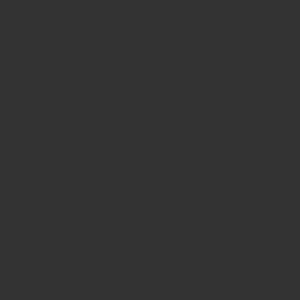
製品内圧不足で起きる不良としては、製品表面の転写不足やヒケ、ボイドが上げられます。保圧を上げることで圧力損失を緩和し、対処できる時もありますが、保圧で対処できない時もあります。保圧を上げ続けると、型締め力が足りなくなり、バリが発生することもあります。また、保圧を上げ続けてもバリが出なくても、ヒケやボイドが直らないことがあります。それは、トンネルゲートのゲートシールが速いため、製品内圧が早くに減少に転じるため、圧力不足が起き、ヒケやボイドが発生します。
設計段階で、製品内圧の状態を調べるには、流動解析ソフトが必要となってきます。経験的に、内圧不足を起こさないよう、最初から肉厚部分を極力なくすような製品設計にすることや、最悪、サイドゲートへの転用ができるように設計するなどの方法も取れますが、流動解析ソフトがあると、このあたりの、試作後の再加工の手間を省くことができます。
今回、内圧不足が原因で起きる不良としてヒケとボイドを上げています。その発生機構として…
- 金型温度が低いと、製品表面層の固化が速いため、遅れて固まる製品内部が表面層に拘束され収縮できないため、真空の気泡が発生します。 ⇒ ボイド
- 金型温度が高いと、製品表面層の固化が遅いため、製品内部の固化と一緒に収縮するため、製品表面が凹みます。 ⇒ ヒケ
まとめ
いかがだったでしょうか。トンネルゲートは、ゲートカット作業を自動で行ってくれる便利なゲート仕様です。ですが、ゲート径が小さくなるため、製品内部の圧力が不足しがちになります。設計段階で、不足しているかどうかは、流動解析ソフトを活用しないと分からないですが、金型を作成してから、再加工する手間を考えると、CAEソフトでの分析を挟んだほうが、費用や手間が減ると考えています。
CAEソフトが無い場合は、経験値とトライアル・アンド・
流動解析では、ランナーの太さや長さ、ゲートの大きさ、ゲート位置や点数の変更が、CADモデルを変更して解析にかけるだけですので、どういったモデルが最良か設計段階で判断することができます。また、樹脂の流動を確認すると、エアーのたまる箇所も分かるため、ベントを設けないといけないことも分かります。ベントが設けられない場合は、射出速度を落とし、焼けを防止しつつ、その部分は製品表面の転写が悪くなることが予測できるため、テカリが許容される箇所なのかどうか、前もって確認することができます。流動解析1つで、とても多くのことが分かりますので、設計してすぐに金型を作成するのではなく、間にCAEソフトでの解析を挟むことをお薦めします。
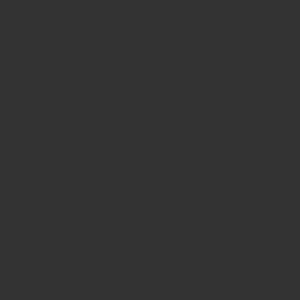